Linear Sensors
Linear potentiometers, magnetical and optical linear transducers and measuring probes
Guide Linear Sensors
Index
Measuring principle of linear sensors
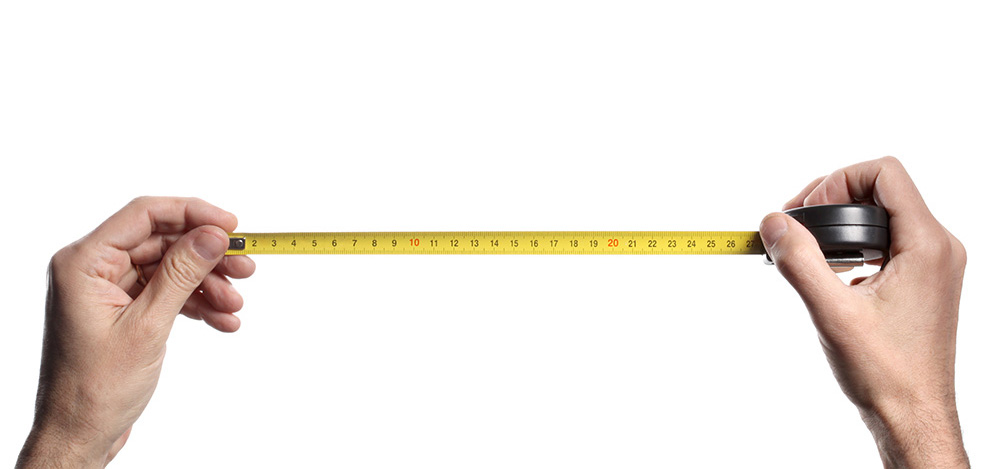
The purpose of displacement sensors is to convert linear motion into electrical signals. To do this, a push rod or a guided or loose actuator is used to mechanically move linearly along the travel path.
In the transducer, the mechanical displacement is detected electrically by a sensor element (electrical measuring path) and converted into electrical signals. The electrical signal acquisition depends on the measuring principle or sensor technology. The acquired signals are either transmitted as analogue signals directly to a transducer for further processing or via internal signal conditioning (measuring amplifier / transducer).
These signals represent the measured path. Displacement measurement systems are used in all areas of industry and medical technology. Wherever linear mechanical movements need to be converted into electrical signals for further processing of control tasks, distance measurement and position detection.
Linear sensor technologies
For linear displacement measurement, linear sensors are available in five different measurement principles:
- Linear potentiometer with potentiometric resistance element
- Magnetostrictive technology
- Inductive technology (LVDT)
- Hall effect technology
- Optical probes with optoelectronic sensor technology
Potentiometric
A linear potentiometer is a passive component whose resistance value can be continuously adjusted. The wiper is moved over the resistance track, which outputs the resistance value depending on its position. The linear potentiometer has three connections: two for the resistor and one for the pick-up.
Application example: injection moulding machines, pneumatics, simple presses
- Simple sensor principle, mostly without electronics
- Measured value is available immediately
- Resolution almost infinite
- Reasonably priced and very many differentiated designs
- Works with low voltages (hardly any power consumption)
- But works with wear
- Sensory characteristics change in the course of operation
- Insensitive to magnetic interference fields
Magnetostrictive
The sensor consists of a robust housing, a waveguide inside, a permanent magnet that deflects the generated pulses and a converter that converts the returning vibrations into an electrical signal. The position of the magnet is then determined by magnetostriction.
Applications include: injection moulding machines, hydraulic cylinders, presses, tank level measurement, rolling mills.
- Sealed sensor (high IP protection) with electronics
- Contactless measuring principle
- Maintenance- and wear-free
- Durable, consistent accuracy
- Long measuring distances up to 4000 mm
- Insensitive to shock and vibration
- Withstands high pressures - ideal for hydraulically moved axes
- Insensitive to many chemical media
- But sensitive to magnetic interference fields
Inductive (LVDT)
The LVDT is an analogue sensor that uses a system of coils - consisting of a primary coil and two secondary coils. These coils convert linear motion into electrical signals.
Application example: probes, quality control, factory automation, food production
- Sealed sensor (high IP protection) with or without electronics
- With very good linearity
- Recording of small measurement changes
- Near infinite resolution
- Durable, consistent accuracy
- Maintenance and wear free
- Suitable for high dynamics
- Reproducible zero point
- Absolute signal output
- Insensitive to many chemicals
- But sensitive to magnetic interference
Hall effect
Hall sensors use a permanent magnet on a moving plunger. One or more Hall ICs are located on the travel path. They measure the field strength along the path and identify the position of the magnet and thus the distance of the measurement path.
Application example: Position detection in elevators or hinges where space is limited.
- Contactless measuring principle
- Maintenance- and wear-free
- Durable, consistent accuracy
- Reliable measurement even with vibration
- Detects wire breaks and short circuits
- Sensitive to magnetic interference
Optoelectronic
There is a glass scale at the end of the pushrod. The transmitter and receiver are positioned opposite each other. The glass scale moves between them. Electrical impulses are converted into light pulses by the transmitter and into electrical signals by the receiver. This is the principle of a glass scale linear encoder. The downstream amplifier compares the received signal with a predetermined switching wave. With our optical probes, precise positions can be detected.
Application example: probes, quality control, dial gauges, precision engineering
- Precise sensor with electronics
- Contactless measuring principle
- Maintenance- and wear-free
- Durable, consistent accuracy
- Very high resolution
- Temperature stable
- Easy mounting
- Insensitive to magnetic interference fields
- But the glass scale is fragile
Technology comparison
Measurement method / Technical requirements | Potentiometric | LVDT | Magnetostrictive | Hall effect | Optoelectronic |
High resolution (100 μm) | + | + | + | + | + |
Very high resolution (1 μm) | - | - | + | + | + |
Operating speed | 0 | 0 | + | + | - |
Small shape | + | + | 0 | + | 0 |
High protection class (IP65) | 0 | 0 | + | + | 0 |
Use in magnetic field | + | - | 0 | - | + |
Very small measuring distances (±1 mm) | - | + | - | 0 | - |
Digital processing required | - | - | - | - | + |
Lateral forces occur (transverse) | 0 | 0 | 0 | - | - |
High measuring rate/strongly oscillating movements | 0 | + | + | + | + |
Electrical interfaces and signals
For a wide range of applications in different industries, we offer displacement sensors with the appropriate electrical interfaces.
Potentiometric and inductive
Our potentiometric and inductive linear sensors have also been designed with integrated electronics to simplify electronic integration. This allows direct connection to typical analogue signals 0...5 V / ±5 V / 0...10 V / ±10 V / 0...20 mA / 4...20 mA without external amplifiers.
Hall effect
Our non-contact Hall sensors have an analogue output of 0.5...4.5V. This allows wire break and short circuit detection.
Magnetostrictive
In magnetostrictive displacement measurement systems, signal processing is always integrated. Electrical connection is via 5, 6 or 8-pin connectors with M12 or M16 threads. Some sensors have an encapsulated cable with a length of one metre (standard) or up to 15 metres on request.
In addition, these sensors offer analogue outputs in voltage or current for direct measurement of displacement and speed, or digital outputs.
Optoelectronic
Incremental displacement measurement outputs count pulses in TTL, OC or LD level.
Mechanical interfaces
Guided push rod with mechanical interfaces
- With spring return as probe
- With ball joints - ideal for compensation of lateral misalignment
- With threaded coupling (with or without return spring)
Loose push rod
- Only for LVDT sensors - with threaded coupling - the application requires a suitably matched interface. Core extensions from 50 mm to 315 mm available as an option
Guided carriage (actuator/cursor)
- Carriage is mechanically or magnetically connected to the displacement sensor, the application requires a correspondingly matched interface
Loose carriage (actuator/cursor)
- The carriage is moved at a defined distance above the surface of the displacement sensor, the application requires a correspondingly adapted interface
There are two types of mechanical integration of pushrods into the displacement sensor:
- The push rod is guided on both sides. This means that the push rod 'protrudes' horizontally in both directions of the sensor housing. This provides greater robustness in miniaturized displacement sensors, as the push rod is safely linearly guided in both bearings. It also eliminates the need for complex bearing arrangements.
- The push rod is guided on one side. This means that the connecting rod only protrudes on the measuring side. Bearings inside the housing give stability to the push rod.
Mounting
We offer a wide range of installation accessories depending on the product and application. Many accessories are included with the sensor. Please also refer to our information on the product datasheets.
As a general rule: Each sensor requires a clean and flat mounting surface. For longer measurement distances, additional support should be considered to prevent deflection. Do not subject the sensor housing to mechanical stress.
Many sensors are already supplied with fixing clamps. Some have mounting blocks, flanges or ball joints.
Our displacement sensors are designed to be space-saving, robust and accurate. With our linear sensors you can measure mechanical distances up to 4000 mm. A wide range of mechanical and electrical interfaces allow the best possible design and electrical integration into your application.
We meet the most demanding requirements in terms of protection class, EMC, shock, hydraulic pressure (up to 350 bar), accuracy (up to 1 µm) and measurement dynamics (up to 10 m/s @ max. 100 m/s²). Each measurement principle has its own advantages, which we will discuss with you.
The requirements of the application determine the choice of transducer. In many cases, demanding applications require technical product adaptation. MEGATRON is your specialist for this adaptation process - even for small quantities.